显微镜下的质量控制
为什么电池制造商要了解激光诱导击穿光谱(LIBS)?

电池制造商要不断提高产能。他们需要以经济、高效和可靠的方式保证质量。检测锂离子电池中的杂质时,通常要用到扫描电子显微镜(SEM)和能量色散X射线谱仪(EDS/EDX)。SEM/EDS操作起来复杂、耗时,难以集成到生产中。近期,一种新方法通过利用光学显微镜和激光诱导击穿光谱(LIBS),可支持同时进行视觉和化学分析,以提高QA/QC的效率。
引言
2019年,全球锂离子(Li-Ion)电池市场价值为329亿美元,从2020年到2027年,这一数字预计将以13.0%的复合年增长率(CAGR)持续增长[1]。电动汽车需求的快速增长是推动市场发展的重要因素,但不是wei yi因素,其他因素包括可再生能源装置日益普及(如光伏板),各种医疗设备广泛采用锂离子电池,以及便携式消费电子产品的市场逐步扩大。
锂离子电池的性能提升后,越来越受各行各业的市场欢迎,但自身也遇到了发展瓶颈。人们仍然担心锂离子电池过热的问题,特别是当充电过快时。电动汽车必须快速充电,因此这方面的安全性非常重要。锂离子电池的寿命通常较短,许多锂离子电池的充电/放电周期不足1,000次[2,3]。
这些问题大多可以在制造过程的质量控制阶段成功解决。电池在使用过程中过热,往往是因为电极、燃料电池分离器和锂离子电池的其他部件中存在的金属颗粒。这些颗粒会导致内部短路,从而引起过热,降低电池容量和寿命,甚至在ji duan情况下会引发火灾[4-6]。
市场对相关产品的需求急剧上升,因此电池制造商既希望QA/QC程序足够高效,能够捕获这些杂质;但又不至于太过繁琐,以免拖慢制造过程或产生大量额外成本。
技术挑战
制造商检测锂离子电池中杂质的既定方法复杂、耗时,而且很难整合到生产线上,这是他们面临的一大难题[7]。
在工业制造环境中,搭载扫描电子显微镜(SEM)的能量色散X射线谱仪(EDS)是常用的质量控制设备。研究人员可借助SEM-EDS,利用一种能生成高分辨率、高对比度图像的显微镜技术对材料进行目视检查,并通过元素光谱分析确定其局部成分。
SEM-EDS通常需要制备特殊样品,并将样品转移到真空中进行观察和分析——这个过程比较耗时,而且技术难度不小。在电池制造和质量控制中,SEM-EDS在检测锂(Li)方面也存在操作缺陷,而锂元素则是可充电电池技术最重要的元素[7]。此外,由于SEM-EDS是一种复杂的成像方法,因此很难直接整合到生产线中。样品需要被送出生产线进行分析,几个小时甚至几天后才能得到分析结果,这拖慢了生产过程、浪费了时间、推高了成本。
X射线荧光(XRF)和辉光放电发射光谱法(GD-OES)更便于整合到生产线中,但也有其他缺点。XRF不能准确检测锂等轻元素[8,9],而GD-OES往往会严重损坏样品,并且不适用于检测绝缘材料[9-11]。
新技术
一种新方法正在电池制造和其他工业应用中崭露头角:将光学显微镜和激光诱导击穿光谱(或LIBS)结合起来,在更短的时间内获得视觉和化学样品信息。
LIBS可用于分析材料成分,高能量激光脉冲会击中材料表面的目标区域,能量经过吸收后,导致局部区域被烧蚀并形成凹口。等离子体经过诱发,然后立即分解,从而发射出光,此时检测元素线光谱,即可确定元素。
这种方法无需使用扫描电镜,所以可省去许多耗时的步骤:分析前无需额外制备样品;样品无需在真空中观察,所以空气中的干或湿样品都可以分析;而且待样品转移后,无需重新定位样品上的感兴趣区域或调整系统。结果数秒内即可生成,因此质控过程中的分析环节可以快速完成,无需借助于实验室——成本也因此大幅下降。
近年来,Leica Microsystems在该领域投入了大量的时间和资源,因为我们很看好这项技术的前景。时效和准确性对长期成功至关重要。Leica Microsystems的DM6 M LIBS系统专为电池制造等工业应用而设计,能更快地提供结果。
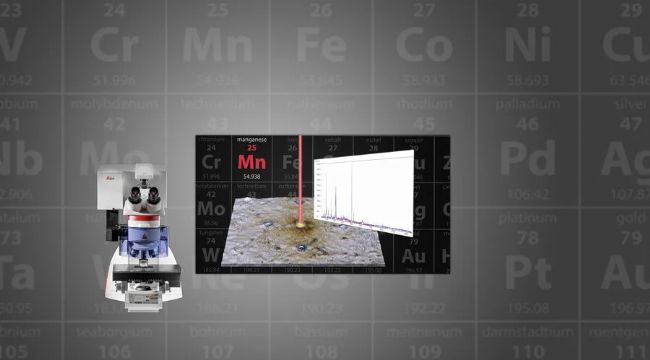
走向未来
许多行业还没有接受LIBS,也许是因为SEM-EDS、XRF或GD-OES还是目前gong ren的解决方案。的确,在各行各业的产品开发、质量控制和故障分析中(特别是在电池制造中),获得可靠的结果和理想的产品质量始终是重中之重。但是,工业制造商绝不能让“试过,但没成功”的想法阻碍进步,或否认大胆尝试在提升生产力和盈利能力方面的巨大作用。SEM-EDS和其他技术在某些应用中仍有很大的价值,但面对快速变化的生产节奏,要想确保质量控制始终快速、准确,制造商就应该考虑启用光学显微镜和LIBS——等他们看到新方法的优势时,他们将庆幸自己做出了正确的选择。
原文发表于2021年4月13日《电气工程》。
参考文献
Lithium-ion Battery Market Size, Share & Trends Analysis Report By Product (LCO, LFP, NCA, LMO, LTO, Lithium Nickel Manganese Cobalt), By Application, By Region, And Segment Forecasts, 2020 – 2027 (Grand View Research, July, 2020) Report ID: GVR-1-68038-601-1.
K.A. Severson, P.M. Attia, N. Jin, N. Perkins, B. Jiang, Z. Yang, M.H. Chen, M. Aykol, P.K. Herring, D. Fraggedakis, M.Z. Bazant, S.J. Harris, W.C. Chueh, R.D. Braatz, Data-driven prediction of battery cycle life before capacity degradation, Nature Energy (2019) vol. 4, pp. 383–391, DOI: 10.1038/s41560-019-0356-8.
M.‐W. Cheng, Y.‐S. Lee, M. Liu, C.‐C. Sun, State‐of‐charge estimation with aging effect and correction for lithium‐ion battery, IET Electrical Systems in Transportation (2015) vol. 5, iss. 2, pp. 70-76, DOI: 10.1049/iet-est.2013.0007.
X. Feng, M. Ouyang, X. Liu, L. Lu, Y. Xia, X. He, Thermal runaway mechanism of lithium ion battery for electric vehicles: A review, Energy Storage Materials (2018) vol. 10, pp. 246-267, DOI: 10.1016/j.ensm.2017.05.013.
D.P. Finegan, M. Scheel, J.B. Robinson, B. Tjaden, I. Hunt, T.J. Mason, J. Millichamp, M. Di Michiel, G.J. Offer, G. Hinds, D.J.L. Brett, P.R. Shearing, In-operando high-speed tomography of lithium-ion batteries during thermal runaway, Nature Communications (2015) vol. 6, art. num. 6924, DOI: 10.1038/ncomms7924.
E.V. Beletskii, A.A. Fedorova, D.A. Lukyanov, A.Y. Kalnin, V.A. Ershov, S.E. Danilov, D.V. Spiridonova, E.V. Alekseeva, O.V. Levin, Switchable resistance conducting-polymer layer for Li-ion battery overcharge protection, Journal of Power Sources (2021) vol. 490, 229548, DOI: 10.1016/j.jpowsour.2021.229548.
P. Hovington, V. Timoshevskii, S. Burgess, H. Demers, P. Statham, R. Gauvin, K. Zaghib, Can we detect Li K X‐ray in lithium compounds using energy dispersive spectroscopy? Scanning (2016) vol. 38, iss. 6, pp. 571-578, DOI: 10.1002/sca.21302.
P. Kikongi, J. Salvas, R. Gosselin, Curve‐fitting regression: improving light element quantification with XRF, X-Ray Spectrometry Special Issue: European Conference on X‐Ray Spectrometry 2016 Part 2 (2017) vol. 46, iss. 5, pp. 347-355, DOI: 10.1002/xrs.2760.
M.J. Lance, D.N. Leonard, B.A. Pint, The Use of Glow Discharge Optical Emission Spectroscopy to Quantify Internal Carburization in Supercritical CO2, 6th International Supercritical CO2 Power Cycles Symposium, 27 - 29 March, 2018, Pittsburgh, PA, USA.
R.K. Marcus, A.B. Anfone, W. Luesaiwong, T.A. Hill, D. Perahia, K. Shimizu, Radio frequency glow discharge optical emission spectroscopy: a new weapon in the depth profiling arsenal, Anal. Bioanal. Chem. (2002) vol. 373, pp. 656–663, DOI: 10.1007/s00216-002-1378-8.
M. Wilke, G. Teichert, R. Gemma, A. Pundt, R. Kirchheim, H. Romanus, P. Schaaf, Glow discharge optical emission spectroscopy for accurate and well resolved analysis of coatings and thin films, Thin Solid Films (2011) vol. 520, iss. 5, pp. 1660-1667, DOI: 10.1016/j.tsf.2011.07.058.
免责声明
- 凡本网注明“来源:化工仪器网”的所有作品,均为浙江兴旺宝明通网络有限公司-化工仪器网合法拥有版权或有权使用的作品,未经本网授权不得转载、摘编或利用其他方式使用上述作品。已经本网授权使用作品的,应在授权范围内使用,并注明“来源:化工仪器网”。违反上述声明者,本网将追究其相关法律责任。
- 本网转载并注明自其他来源(非化工仪器网)的作品,目的在于传递更多信息,并不代表本网赞同其观点和对其真实性负责,不承担此类作品侵权行为的直接责任及连带责任。其他媒体、网站或个人从本网转载时,必须保留本网注明的作品第一来源,并自负版权等法律责任。
- 如涉及作品内容、版权等问题,请在作品发表之日起一周内与本网联系,否则视为放弃相关权利。